Maintenance prédictive et capteurs
La maintenance prédictive révolutionne la manière d’entretenir les équipements industriels. Grâce à l’analyse continue de données issues de capteurs (température, vibration, courant, humidité, etc.), elle permet de détecter les signes précurseurs de défaillance bien avant qu’une panne ne survienne.
Prévoyez les pannes avant qu’elles ne surviennent : La maintenance prédictive avec capteurs : votre meilleur allié contre les arrêts imprévus.
Planifiez une évaluation
Pourquoi la maintenance prédictive ?
Cette approche intelligente réduit les arrêts non planifiés, prolonge la durée de vie des machines et optimise les coûts d’entretien. Chez Ziustek, nous intégrons des solutions de maintenance prédictive adaptées à votre réalité industrielle, pour des opérations plus fiables, plus sûres et plus rentables.
✅ Évite les arrêts de production
✅ Allonge la durée de vie des équipements
✅ Réduit les coûts de maintenance non planifiée
✅ Optimise la gestion des pièces de rechange
✅ Prévient les accidents et défaillances critiques
Comment ça fonctionne ?
Comment ça fonctionne – Partie 1 : la collecte de données
La maintenance prédictive repose d’abord sur la collecte continue de données en temps réel grâce à des capteurs installés sur les équipements critiques. Ces capteurs mesurent des paramètres clés tels que les vibrations, la température, le courant électrique, la pression, ou encore l’humidité. Les données sont ensuite transmises à une plateforme d’analyse, localement ou dans le cloud, pour être comparées à des seuils prédéfinis ou à des modèles de comportement normal.
Du capteur à la décision
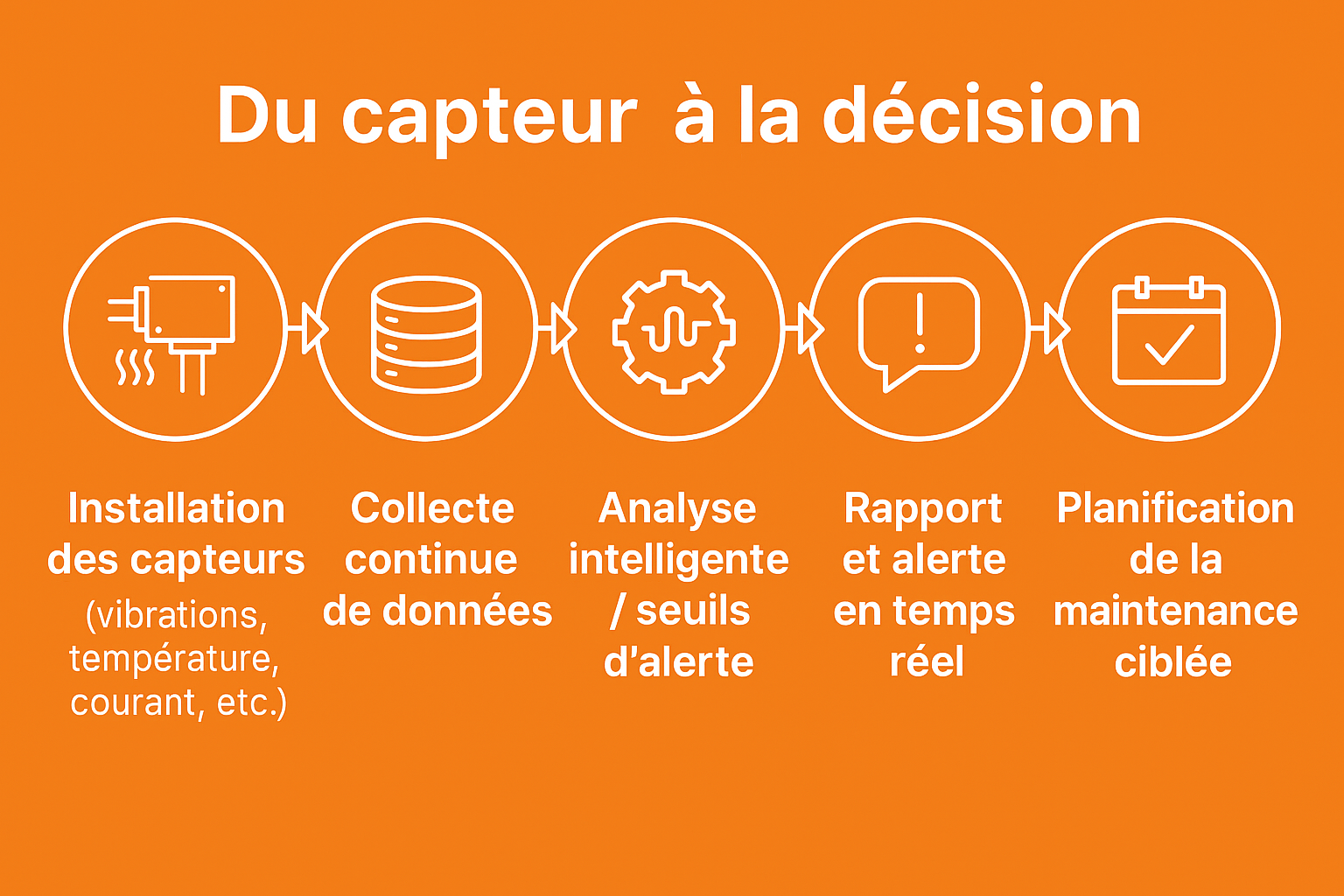
Types de capteurs utilisés
🔧 Vibrations – détecter les déséquilibres mécaniques
🌡️ Température – surveiller les hausses anormales
⚡ Courant/puissance – identifier une consommation irrégulière
💨 Pression – contrôler les systèmes pneumatiques ou hydrauliques
💦 Humidité – pour les environnements sensibles
🎧 Ultrasons / acoustiques – pour détection précoce d’usure
Gagner du temps en découvrant des innovations en ingénierie, visitez https://www.machinedesign.com/
Comment ça fonctionne – Partie 2 : l’analyse et l’anticipation
Une fois les données collectées, des algorithmes ou des systèmes d’intelligence artificielle analysent les variations et détectent les signes avant-coureurs d’anomalies. Lorsqu’un écart significatif est identifié — par exemple une augmentation anormale de vibrations — une alerte est générée pour prévenir l’équipe de maintenance. Cette approche permet d’intervenir au bon moment, avant la panne, évitant ainsi des arrêts coûteux, des bris majeurs ou des pertes de production.
Après l’analyse des données collectées, la maintenance prédictive entre dans sa phase la plus stratégique : l’interprétation intelligente et la prise de décision. Grâce à des algorithmes avancés ou à des seuils définis, le système identifie les écarts significatifs par rapport au comportement normal des équipements.
Vos bénéfices (Ce que vous gagnez concrètement)
Ces écarts déclenchent des alertes ou des recommandations d’intervention ciblée. Cela permet aux équipes techniques d’agir au bon moment, sur le bon composant, avec les bonnes ressources, évitant ainsi les pannes graves et les arrêts imprévus. Cette capacité à anticiper permet aussi de mieux planifier l’inventaire de pièces de rechange et les horaires des équipes de maintenance. En somme, chaque décision est appuyée par des données fiables, réduisant les imprévus tout en augmentant la rentabilité de l’usine.
📉 Diminution des arrêts non planifiés
🔄 Entretien basé sur l’état réel, pas le calendrier
🧠 Décision proactive au lieu de réactive
💰 Retour sur investissement rapide
🛡️ Fiabilité accrue de vos lignes critiques
Adopter la maintenance prédictive, c’est transformer la façon dont vous entretenez vos équipements. Cette approche permet de réduire significativement les arrêts non planifiés, d’allonger la durée de vie des machines et de diminuer les coûts d’entretien en évitant les interventions inutiles. Elle améliore également la sécurité des opérations en détectant les défaillances avant qu’elles ne deviennent critiques, tout en optimisant la planification des ressources et la disponibilité des pièces. En un mot, c’est un levier concret pour accroître la performance globale de votre production.